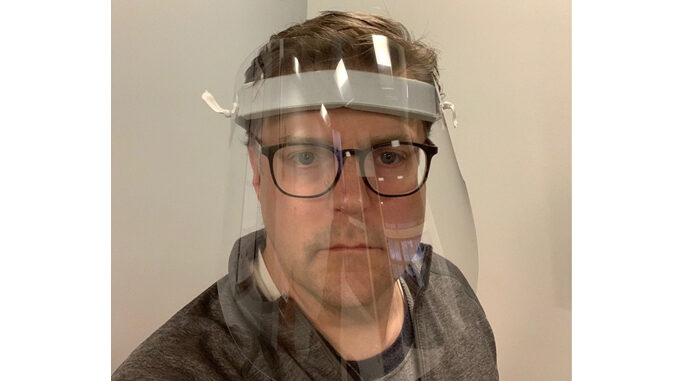
Known for live event, entertainment, and scenic production, Production Resource Group (PRG), LLC, in New Windsor, is switching tracks to manufacture face shields for health workers on the front lines of the COVID-19 crisis.
“Around mid-March, as the Coronavirus outbreak really started to affect business, one of my project managers, Alvin DeLeon, came to me to discuss what we might be able to do as a company to assist in the emergency medical supplies needs across the nation,” said Mark Peterson, general manager, PRG Scenic Technologies. “He and I started researching what kinds of products that we might be able to fabricate quickly and easily without a tremendous amount of re-fitting of the shop. Face shields, temporary hospital beds, and isolation booths were on the top of our list. It just so happened that as we were narrowing down what we thought we could produce the call came in from my friend.”
The friend was someone who works for another scenic shop. He was helping New York University put together a team of shops to help fabricate face shields to support the New York City medical community.
Once the decision was made to manufacture face shields, PRG’s design had to be vetted by the NYC Department of Health. The company then had to figure out what labor and materials would be necessary for the quantity it committed to providing.
“Materials are the hardest part of the process,” Peterson said. “Everyone seems to be making these face shields. I think that’s because they are relatively simple and low risk to make.”
PRG brought back 18 employees to assist in the effort, but Peterson additional workforce would be added as the demand increases.
“The great thing about PRG as a company is that we have facilities across the globe so if the demand is there we could convert our facilities to help the effort in all corners of the globe.”
The face shield design is a slight modification to the Open Source design circulated by Uriel Eisen.
“I felt that if I was going to get into the medical supply business that I needed to develop a manufacturing process that protected the workers in the shop by providing them with appropriate PPE and following safe distancing work rules, as well as make sure that our products were safe and uncontaminated for the health care workers that needed to use these products,” Peterson said. “I think what sets us apart is that we have made sure that our plastics meet FDA guidelines, and our foam pads, and elastic banding meet flammability ratings that meet the regulations for medical splash guards and clothing.”
They’re fairly simple and only required a couple of routed parts, some elastic, and a piece of foam. The shields take about two to two-and-a-half minutes to assemble and package.
Having only started production recently, Peterson said he expects the facility will be able to create 15,000 shields per week with over 60,000 manufactured across three facilities.
Each bag of face shields will be labeled with a serial number so problems can quickly be identified down the road. This initial order will be delivered to NYC, but other orders will be shipped wherever they are needed.
“It’s a great honor to be able to help in any small way we can,” Peterson said. “My goals are three-fold: First to help the City of New York and its medical community in this fight, secondly to get some of our employees back to work so they can better support their families, and third to support PRG through these challenging times.”